When selecting an air compressor for a pulse bag dust collector, it’s essential to consider several key factors to ensure optimal performance. Below are the primary aspects to consider:
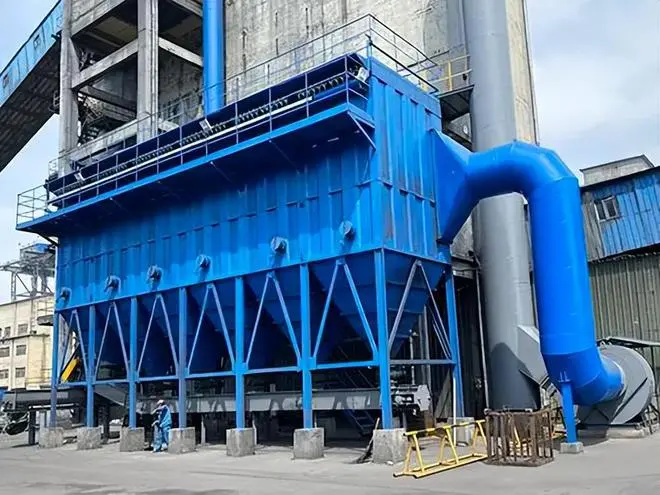
1. Compressor and Supporting Equipment Selection
The air compressor should match the specific gas requirements of the pulse dust collector. Key considerations include:
- Oil Removal: To reduce oil content in the compressed air, an oil-removal purifier can be used. For higher treatment standards, multi-stage purification may be necessary.
- Water Removal: To reduce water content in the compressed air, water removal equipment should be installed. This helps to ensure dry air, which is crucial for maintaining the efficiency of the pulse bag dust collector.
2. Selection of Compressor Structure
The type of compressor (vertical, horizontal, or angled) should be chosen based on the production needs of the pulse bag dust collector and the specific layout of the facility. This selection can impact the overall space utilization and operational efficiency of the system.
3. Determining the Appropriate Compressor Model
The exhaust volume and exhaust pressure required for the pulse bag dust collector will determine the right compressor model. It’s essential to select a model based on the compressor specifications provided in product catalogs, noting that:
- Exhaust Volume: This is typically listed at 20°C and 101.33 kPa and expressed in m³/min.
- Exhaust Pressure: This is expressed in Pa (gauge pressure) and must align with the operational needs of the pulse dust collector.
Considerations for Air Compressor Performance:
- Exhaust Pressure: A higher exhaust pressure consumes more energy. The compressor should be selected based on the operating pressure, pipeline resistance, and pressure of supporting equipment. It’s recommended to select a larger diameter gas pipeline to reduce resistance and improve energy efficiency during long-term operation.
- Exhaust Volume: Calculate the actual total gas consumption and multiply it by a factor of 1.1 to 1.2 to determine the required exhaust volume. If the selected compressor’s exhaust volume is too low, it will fail to meet the needs of the pulse dust collector. Conversely, choosing a compressor with too high an exhaust volume will lead to unnecessary energy consumption and increased operating costs.
4. Pre-Purchase Considerations
Before purchasing an air compressor, it’s essential to carefully evaluate the requirements to avoid issues during use. The calculation for compressed air consumption is based on the pulse valve consumption and lift valve consumption. For dust collectors, the primary compressed air consumption is for dust cleaning by the electromagnetic pulse valve.
The most common calculation formula for compressed air consumption is as follows:
Air Consumption (L)=1.5×n×Q/T
Where:
- 1.5 is a margin for safety.
- n is the air consumption of a single dust collector, which depends on the pulse valve size, injection time interval (affected by dust viscosity), injection pressure, pulse width, and other related factors.
- Q is the single injection air volume of a single valve.
- T is the injection cycle.
For example, a typical 3-inch submerged valve might have a single injection air volume of 250-300 liters (depending on pressure and diaphragm opening time).
5. Air Compressor Type
Most air compressors used for pulse dust collectors are either piston or screw compressors. While oil-free air compressors are a good option, most manufacturers do not support them due to higher costs. Regardless of the type chosen, it’s important that the compressor be paired with an air tank, dryer, and filter to remove oil and moisture from the air. Even though oil-free compressors don’t pose an oil contamination risk, they still contain moisture, requiring post-processing equipment to ensure air quality.
Conclusion
In summary, selecting the correct air compressor for a pulse bag dust collector is essential for achieving optimal performance and energy efficiency. By taking into account the exhaust volume, exhaust pressure, compressor type, and necessary post-processing equipment, you can ensure that the compressor meets the specific needs of your dust collection system. A well-chosen air compressor for a pulse bag dust collector not only enhances dust cleaning efficiency but also contributes to reduced operating costs and improved system longevity. Therefore, careful consideration during the selection process is key to maintaining smooth and effective operations.