Sealant is a substance used to block the passage of fluids through openings in materials, a type of mechanical seal. In building construction, sealant is synonymous with caulk and also serve the purposes of blocking dust, sound and heat transmission.
The strength of sealant prepolymers is not very high, so fillers with certain reinforcing effects must be added. Common fillers include calcium carbonate, quartz powder, carbon black, titanium dioxide, aluminum hydroxide, talc, kaolin, clay, and others. Among these, calcium carbonate fillers have many advantages. It has multiple particle size classifications, various surface treatment methods, high whiteness, mature production technology, and a low price. Compared to other fillers, it is the most widely used.
Calcium carbonate in sealants
The advantages of calcium carbonate in sealants are that it can increase the volume of the sealant and improve its tensile strength, wear resistance, tear resistance, hardness, and more. The amount of calcium carbonate added can account for 10% to 70% of the entire sealant formulation. Due to the large quantity of calcium carbonate used in sealants, the sealant industry has also raised higher requirements for calcium carbonate products. Stable quality, small fluctuations in various performance indicators, good reinforcing effect and processing performance, a suitable price, and the ability to generate certain economic benefits are all very important.
Currently, domestic calcium carbonate has gradually overcome various technical difficulties, replaced imported calcium carbonate products with excellent product quality. The development of the sealant field has promoted the growth of the entire calcium carbonate industry. The two industries complement each other and are closely related.
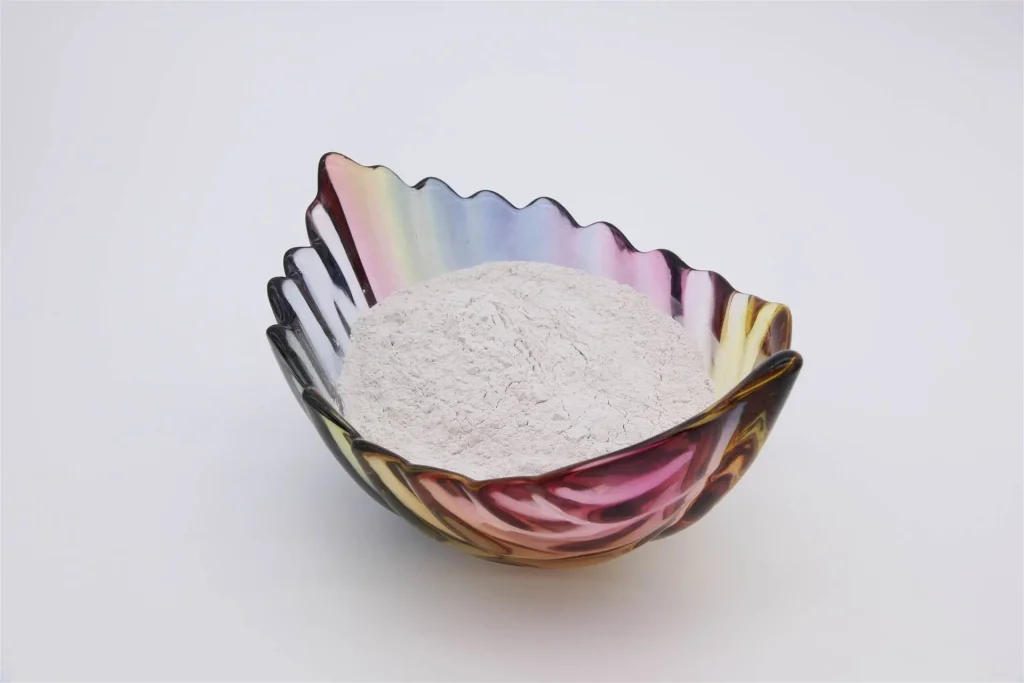
Differences of calcium carbonate
Typeshere are three main types of calcium carbonate products: nano calcium carbonate, light calcium carbonate, and heavy calcium carbonate. R&D personnel need to make reasonable choices based on the performance requirements of the sealant. When preparing leveling sealants like potting compounds, calcium carbonate with a large particle size and good fluidity can be selected. For sealants with high thixotropy requirements, calcium carbonate with a small particle size and surface treatment can be chosen. When preparing high-hardness sealants, the amount of calcium carbonate added can be appropriately increased. To improve extrusion properties, nano calcium carbonate and heavy calcium carbonate can be used in combination.
Additionally, differences in particle size, oil absorption value, moisture content, surface activation method, and activator selection can result in significant variations in the physical and mechanical properties of sealants. For example, by studying the effect of calcium carbonate on the performance of two-component silicone sealant, we can provide valuable reference information for selecting calcium carbonate in sealants.
Silicone sealants are divided into two components: base glue (Component A) and curing agent (Component B).
Component A: Add 120 parts of 107 silicone rubber and 100 parts of calcium carbonate to a double planetary mixer and mix thoroughly. Then, transfer the mixture into a clean container and seal.
Component B: Add the curing agent to a double planetary mixer, mix well, and then transfer it into a clean plastic tube and seal.
Detailed information on calcium carbonate products from six manufacturers is shown below:
Table 1: Detailed information on calcium carbonate products from different manufacturers.
Moisture Content of Calcium Carbonate
The moisture content test results of calcium carbonate products from different manufacturers are shown in Table 2.
Table 2: Moisture content of calcium carbonate products from different manufacturers
As shown in Table 2, the moisture content of all calcium carbonate samples detected after entering the factory is higher than the value provided by the manufacturer to some extent. This is because calcium carbonate easily absorbs moisture during transportation. When the moisture absorption reaches a certain level, a local microscopic network structure with calcium carbonate as the node will form. In severe cases, local microstructuring and stress concentration may occur in the sealant, leading to the formation of a large number of evenly distributed fine “particles,” which manifest as local shrinkage or protrusions. Therefore, during sealant production, a dehydration process is required in the mixing phase. For moisture-curing sealants, the calcium carbonate must be dried before incorporation to avoid affecting the storage stability of the sealant.
Effect of Different Calcium Carbonates on Sealant Viscosity
After the prepared sealant component A was placed under standard conditions for 24 hours, its viscosity was tested using a rotational viscometer. The test results are shown in Table 3.
Table 3: Viscosity of Component A
It can be seen from Table 3 that for calcium carbonate products with similar particle sizes, the viscosity of the sealants made from them is also similar. Among the 6 sealant products, the viscosity of the sealants made from 5# and 6# calcium carbonate is slightly lower, which is due to the larger particle sizes of the two.
Effect of different calcium carbonates on the fluidity of sealants
The fluidity test results of sealants are shown in Table 4.
Table 4 Fluidity of sealant
From the results in Table 4, it can be seen that the sealants prepared with 1# and 2# calcium carbonate do not flow, while the sealants prepared with 3#-6# calcium carbonate all exhibit good fluidity. In other words, the sealants made with nano calcium carbonate have good thixotropy, while those made with light and heavy calcium carbonate have good leveling properties. Thus, the size of the calcium carbonate particles determines the thixotropy and leveling properties of the sealant.
Effect of different calcium carbonates on sealant hardness
The sealant hardness test results are shown in Table 5.
Table 5 Sealant hardness
Effect of Different Calcium Carbonates on the Mechanical Properties of Sealants Under Standard Conditions
The data presented in Table 5 shows that the sealants prepared using 5# and 6# heavy calcium carbonate exhibit lower hardness, while those prepared with 1#-4# calcium carbonate demonstrate higher hardness. This difference can be attributed to the surface treatment of the calcium carbonate. Calcium carbonate treated with fatty acids forms numerous physical crosslinking points, thereby increasing the hardness of the resulting sealant. In contrast, the heavy calcium carbonate, which lacks surface treatment, influences the sealant’s hardness based on its intrinsic hardness.
Mechanical Properties of Sealants Under Standard Conditions
The A and B components of the sealant were mixed in a mass ratio of 12 : 1 and allowed to cure for 14 days under standard conditions [temperature: (23 ± 2) °C, relative humidity: (50 ± 5)%]. A sheet with a thickness of (2.0 ± 0.2) mm was formed after mixing. The mechanical properties, including tensile strength and elongation at break, were then tested following the GB/T 528-2009 standard. In addition, high-temperature and low-temperature tests were conducted to evaluate the sealant’s performance under extreme conditions. For the high-temperature test, the sample was placed in a 90°C oven for 168 hours, followed by a tensile test. For the low-temperature test, the sample was subjected to -30°C for 168 hours before the tensile test.
Table 6 The results of the mechanical property tests under standard conditions are summarized
Tensile Strength and Elongation at Break of Sealants Made with Different Calcium Carbonates
As shown in Table 6, the six types of silicone sealants made with different calcium carbonates exhibit varying tensile strength and elongation at break after vulcanization. Specifically:
- The tensile strength and elongation at break of sealants made with 1# and 2# calcium carbonate are similar.
- The tensile strength and elongation at break of sealants made with 3# and 4# calcium carbonate are also comparable.
- The tensile strength and elongation at break of sealants made with 5# and 6# calcium carbonate are close to each other.
Calcium carbonates 1# and 2# are nano-sized, with particle sizes around 50 nm and a large specific surface area. These nano-calcium carbonates have many contact points (reinforcement sites) with the polymer matrix of the sealant, facilitating strong interactions at the molecular interface. This improves the sealant’s toughness, impact resistance, and tear resistance by preventing crack propagation, generating shear bands, and absorbing energy, thus enhancing both tensile strength and elongation.
Calcium carbonates 3# and 4# are micron-sized active lightweight powders, with a specific surface area only slightly smaller than that of the nano-calcium carbonates. Their reinforcement effect is similar, but slightly less effective than that of nano-calcium carbonate, due to fewer reinforcement points.
Calcium carbonates 5# and 6# are active heavy calcium powders with a significantly smaller specific surface area compared to nano and active light calcium carbonates. These powders offer the fewest reinforcement points, resulting in the lowest tensile strength and elongation at break, and the weakest reinforcement effect.
Mechanical properties of sealant under 90 ℃ high temperature conditions
The test results of the mechanical properties of sealant under 90 ℃ high temperature conditions are shown in Table 7.
Table 7 Mechanical properties of sealant under 90 ℃ high temperature conditions
After high-temperature treatment at 90°C, the tensile strength and elongation at break of the sealant are significantly reduced. Among all, those made with 1# and 2# nano calcium carbonate exhibit the most substantial decreases in strength and elongation. This is attributed to the large specific surface area of nano calcium carbonate, which results in a larger heating area. As a result, its reinforcement effect is more sensitive to high-temperature treatment, leading to a greater reduction in mechanical properties.
Mechanical Properties of Sealants Under Low-Temperature Conditions of -30°C
The test results for the mechanical properties of sealants under low-temperature conditions of -30°C are shown in Table 8. Compared to the standard conditions, the tensile strength and elongation at break of several sealants have increased to varying extents. The reasons for this unexpected result warrant further investigation and confirmation.
Table 8 Mechanical properties of sealant at low temperature of 30 ℃
Conclusion
Different types of calcium carbonate have distinct effects on the performance of sealants. Nano calcium carbonate, with its small particle size, provides the best reinforcement, resulting in sealant products. It also has excellent thixotropy and the highest tensile strength and elongation at break. Light calcium carbonate and heavy calcium carbonate, with slightly larger particle sizes, offer a less effective reinforcement compared to nano calcium carbonate. But the sealants made from them exhibit good fluidity. Sealants made with light calcium carbonate have the highest hardness. Those made with heavy calcium carbonate have the lowest hardness.
Both high-temperature and low-temperature treatments affect the mechanical properties of silicone sealants. After high-temperature exposure, the tensile strength and elongation of sealants made with different calcium carbonates decrease. Conversely, after low-temperature exposure, these properties increase across the different types of calcium carbonate-based sealants.