Multi-Rotor Dryer Mill
Multi-layer grinding head, strong shearing force and dispersing force.
Surface modification of mineral powder is an inevitable product of the development of modern high-tech and new materials.
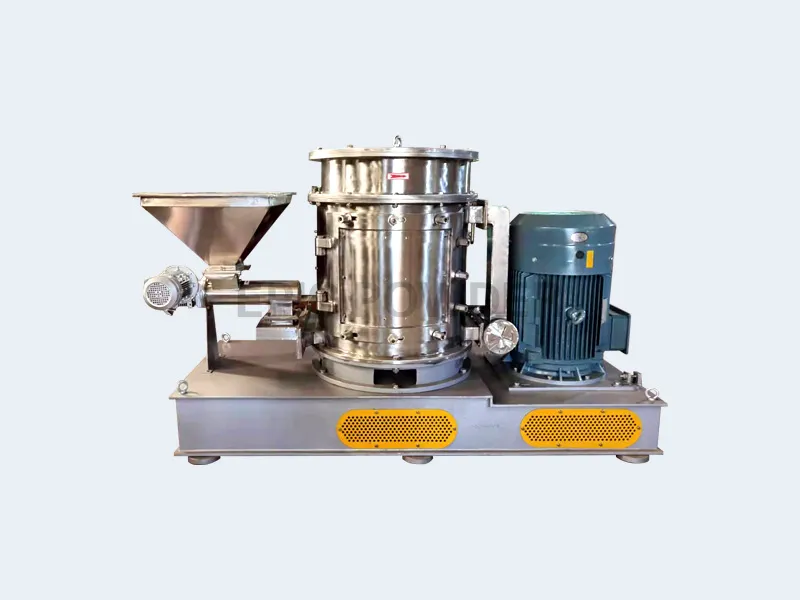
Working Principle
The modifier adopts measures such as dilution, emulsification, spray addition, etc. to improve the dispersion and the spray or drip method linked with continuous powder feeding will achieve better results.
The control of process temperature and time should meet the modification mechanism or the requirements of the modifier on the process conditions to ensure the adequacy of the modification reaction or coating.
The precise metering and uniform addition and feeding of modifiers and materials ensure the instantaneous accuracy of the ratio of the two.
Other factors, such as the use of auxiliary equipment, breakers or classifiers, environmental factors (temperature, humidity), etc.
Features And Benefits
- Powder surface modification machine is widely used in non-metallic mineral fillers or pigments, such as modern polymer materials such as plastics, tart glue, adhesives, polymer matrix composite materials, functional materials and coatings and other industries.
- After the mineral powder is modified, it can not only greatly improve the compatibility of inorganic mineral fillers and organic polymers, improve the interface bonding force, enhance the mechanical strength and comprehensive properties of the material, but also greatly improve the performance of powder fillers. The filling amount can reduce the production cost, and at the same time, it can endow the product with some special physical and chemical properties.
- Powder surface modification has important practical significance for improving the performance of the powder, improving its practical value and opening up the development of application fields.
- Surface modification is one of the necessary processing methods for fillers to change from target fillers to functional fillers. It is also the main purpose of mineral filler surface modification.
- High activation degree modification of irregular shape, ultra-light, ultra-fine, viscous, agglomerated materials such as flake needles, under the condition of meeting the modification mechanism and process conditions (the key is the dispersibility of materials and additives), the use of high energy It is a good method to complete the modification during grinding.
Related Products
Technical Parameters
Technical parameters of Multi-Rotor Dryer Mill
MODEL | MRD-1 | MRD-2 | MRD-3 | MRD-4 | MRD-5 | MRD-6 |
---|---|---|---|---|---|---|
Grinding Motor Power(kW) | 45 | 90 | 160 | 200 | 315 | 450 |
Classifying Motor Power (kW) | 5.5 | 7.5 | 15 | 22 | 37 | 55 |
Blade(layer) | 3-6 | 4-7 | 5-8 | 5-8 | 5-8 | 6-10 |
Blade speed(m/s) | 120 | 120 | 120 | 120 | 120 | 120 |
Air volume(m³/h) | 4,500 | 7,000 | 12,000 | 16,000 | 24000 | 36,000 |
Project Cases
A Material Company: Zircon Sand Grinding Equipment
Production Line of Lithium Iron Phosphate for an Electric Vehicle Company in Huizhou
A New Material Company in Zhejiang: Metal powder grinding equipment
Silica soil drying and dispersing modification production line of a mineral products company in Jiangsu
Air Classifying production line of carbon microspheres in a chemical plant in Hubei
A ball milling and modification production line in a calcium carbonate factory in Iran
Latest News
GET IN TOUCH
Our experts will contact you within 6 hours to discuss your needs for machine and processes.
Factory Address:
NO. 369, Road S209, Huanxiu , Qingdao City, China