As an inorganic filler commonly used in plastics, rubber, coatings, and papermaking, the whiteness of calcium carbonate is a key quality indicator. It impacts both the product’s appearance and its market value, as well as its application performance. This article delves into the primary factors influencing the whiteness of calcium carbonate and presents effective solutions.
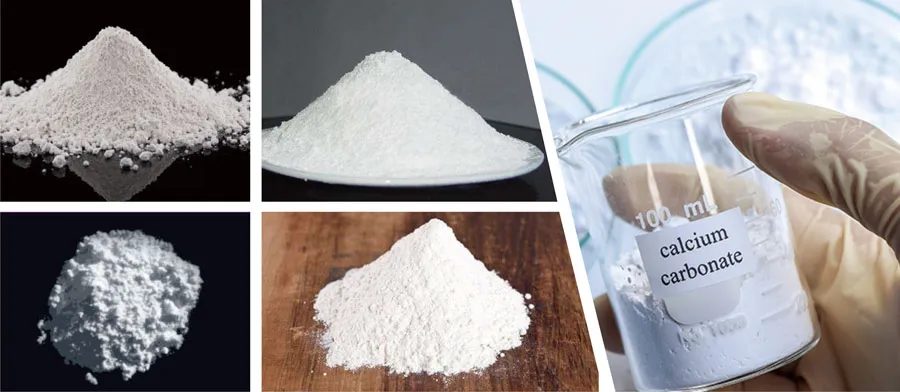
Main Factors Affecting the Whiteness of Calcium Carbonate
1. Quality of Raw Materials
The quality of limestone is a critical factor influencing the whiteness. Impurities such as iron, manganese, and hydrochloric acid-insoluble matter can significantly diminish product whiteness. Typically, calcium carbonate with acceptable whiteness can be produced when iron content in limestone is ≤0.12%, manganese content is ≤0.006%, and hydrochloric acid insoluble content is ≤0.30%. Experienced raw material screeners can often gauge limestone purity by its appearance: limestone that is cyan or light gray generally has higher purity, while those with higher impurity levels may appear yellow, brown, pink, or have patterned or spotted surfaces.
2. Fuel Selection
The choice of fuel in the production of calcium carbonate is also crucial. Impurities such as sulfur and ash present in anthracite coal can directly affect whiteness. For optimal production, the sulfur content of anthracite should be ≤1.5%, ash content should be ≤25%, and other impurities, like soda stone, should be ≤2.0%.
3. Calcining Conditions
The conditions under which quicklime is calcined significantly impact the whiteness. It is essential to control calcination temperature and duration to prevent overburning of quicklime. Additionally, removing impurities such as coke slag and coke core can enhance the whiteness. During the carbonization process, the reaction between Ca(OH)2 and CO2 must be complete to ensure no alkalinization and no agglomeration, thereby improving the dispersion, particle fineness and distribution uniformity of calcium carbonate crystal particles, which also improves the product One of the key pathways to whiteness.
4. Particle Size and Moisture
Particle Size: Generally, a finer particle size of the ore correlates with higher whiteness. However, different mineral products have varying requirements for particle size, necessitating a balanced approach.
Moisture Content: The moisture content of the ore is another critical factor affecting whiteness. Reducing moisture can significantly enhance the whiteness.
Solutions
1. Select High-Quality Raw Materials
Choose limestone with low impurity levels, such as iron and manganese. Ensure raw material purity through rigorous screening and classification. Conduct chemical analyses to confirm that all indicators meet production standards.
2. Optimize Fuel Selection
Use low-sulfur and low-ash anthracite as fuel to minimize its adverse effects on the whiteness of calcium carbonate. Regular quality testing of the fuel is essential to maintain consistency.
3. Improve Production Processes
Calcination Process:
Optimize both the calcination temperature and duration to ensure high-quality quicklime. Enhance calcination efficiency and minimize overburning by upgrading calcination equipment.
Carbonization Process
Improve the purity of kiln gas CO₂ to guarantee complete reaction with Ca(OH)₂. Strengthen monitoring during carbonization to prevent alkalinization and agglomeration.
4. Fine Grinding and Classification
Finely grinding and classifying calcium carbonate enhances the uniformity and fineness of its particles. Using physical methods to improve whiteness is an effective approach to elevating product quality.
5. Chemical Treatment
Employ appropriate chemical treatment methods, such as acid washing and alkaline washing, to eliminate impurities and enhance the purity of calcium carbonate. These treatments can significantly boost whiteness, but it’s crucial to prioritize safety and environmental protection during the process.
6. Adding Additives
Incorporate a suitable amount of whitening agents, such as titanium dioxide, during production to enhance the whiteness of calcium carbonate. Care must be taken regarding the dosage and safety of additives to prevent any adverse effects on product performance.
Conclusion
Several factors influence the whiteness of calcium carbonate, including raw material quality, fuel selection, production processes, particle size, and moisture content. By selecting high-quality raw materials, optimizing fuel choices, improving production methods, fine grinding and classification, applying chemical treatments, and adding effective additives, the whiteness of calcium carbonate can be significantly enhanced to meet market demands for high-quality products. Enterprises should focus on strengthening technological research and development as well as management innovation to continually improve product quality and competitiveness.