Calcium powder (calcium carbonate) is an important additive in PVC products, and its purity significantly impacts their performance. The following is a detailed analysis of the specific effects of calcium powder purity on the performance of PVC products.
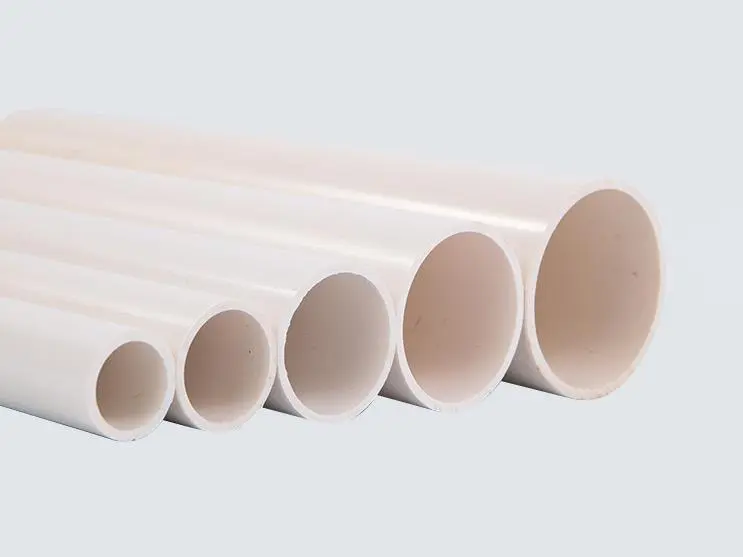
1. Influence on Mechanical Properties
Strength
1) High-purity calcium powder is very beneficial for improving the strength of PVC products. When the purity of calcium powder is higher, its main component can be more evenly dispersed in the PVC resin. Calcium carbonate powder with over 95% purity can closely combine with PVC resin in the production of PVC pipes. When the pipe is subjected to external forces, such as stretching or bending, the calcium powder particles act like tiny “skeletons” that effectively share the external load, thus improving the tensile and bending strength of the pipe. Experimental data show that the tensile strength of PVC products filled with high-purity calcium powder can increase by about 10% to 20%.
2) Low-purity calcium powder contains many impurities that can interfere with the combination of calcium powder and PVC resin. For example, calcium powder with a higher clay content will create an uneven internal structure in PVC products. When subjected to external forces, stress tends to concentrate around these impurities. This can easily lead to cracks and a reduction in the product’s strength.
Hardness
1) High-purity calcium powder can effectively increase the hardness of PVC products. When calcium powder is used as a filler, the higher its purity, the more it enhances the hardness when added to PVC. For example, after adding high-purity calcium powder, the surface hardness of the floor is significantly increased. making it more wear-resistant and able to withstand greater pressure without deformation. This is because high-purity calcium powder can form a denser filling structure in the PVC matrix, limiting the movement of PVC molecular chains and thereby increasing hardness.
2) Low-purity calcium powder may negatively impact the filling effect due to the presence of impurities. Some impurities can weaken the interaction between calcium powder and PVC, resulting in a negligible improvement in the hardness of the filled PVC products.
Density
1) High-purity calcium powder has a higher density. As the calcium powder content increases, the density of PVC products also increases accordingly. While increasing density, high-purity calcium powder can fill the PVC substrate more evenly, reducing voids and defects, thereby improving the overall performance of the product.
2) Impurities in low-purity calcium powder may cause an uneven internal structure in the product, thereby affecting its density and physical properties.
2. Influence of processing performance
In Terms of Fluidity
1) The particle size and shape of high-purity calcium powder are relatively uniform, which enhances the fluidity of the material during PVC processing (such as extrusion, injection molding, etc.). For example, in the extrusion of PVC profiles, high-purity calcium powder allows the material to flow smoothly through the extruder, making it easier to extrude through the mold, resulting in a smoother surface for the extruded profile. This is because the uniform calcium powder particles do not hinder the material’s flow and can form favorable rheological properties with the PVC resin.
2) Low-purity calcium powder may contain metal impurities, such as iron and magnesium. These metal impurities can catalyze the degradation reactions of PVC during processing. At high temperatures, PVC undergoes a dehydrochlorination reaction, and metal impurities can accelerate this process, leading to discoloration and brittleness in PVC products. For instance, calcium powder containing iron impurities can cause PVC to yellow more rapidly during processing and reduce its mechanical properties.
In Terms of Thermal Stability
1) High-purity calcium powder possesses good chemical stability, which benefits the thermal stability of PVC products. During PVC processing, the temperatures are high, and high-purity calcium powder does not decompose or release substances that catalyze the degradation of PVC. For example, during the mixing process of PVC, temperatures usually range between 160-190°C, and high-purity calcium powder does not react adversely with PVC, ensuring smooth processing.
2) Low-purity calcium powder may contain metal impurities, such as iron and magnesium. These metal impurities can catalyze the degradation reactions of PVC during processing. At high temperatures, PVC undergoes a dehydrochlorination reaction, and metal impurities can accelerate this process, leading to discoloration and brittleness in PVC products. For instance, calcium powder containing iron impurities can cause PVC to yellow more rapidly during processing and reduce its mechanical properties.
3. Influence of Chemical Stability
Corrosion Resistance
1) High-purity calcium powder can enhance the chemical stability of PVC products. For example, in outdoor building materials made of PVC (such as PVC door and window frames), products filled with high-purity calcium powder can better resist the erosion from acid rain, chemical fumes, and other corrosive agents. This is because high-purity calcium powder does not introduce other impurities that readily react with corrosive media. Its own chemical properties are stable, and it can form a relatively stable protective layer with PVC. Thereby extending the service life of the product.
2) Impurities in low-purity calcium powder may react with external chemicals. For instance, if calcium powder containing easily oxidizable impurities, these impurities may oxidize when exposed to air. It will trigger chemical reactions that can result in corrosion and discoloration on the surface of the PVC products.
4. Influence on Appearance and Texture
Gloss and Color
1) High-purity calcium powder helps maintain the gloss and color uniformity of PVC products, enhancing their aesthetic appeal.
2) Impurities in low-purity calcium powder can cause spots and color variations on the surface of the products, negatively affecting their appearance quality.
Surface Texture
1) High-purity calcium powder contributes to a more delicate and uniform surface texture in PVC products.
2) Low-purity calcium powder may lead to a rough and uneven surface, reducing the comfort of touch.
In summary, the purity of calcium powder significantly impacts lots of aspects. Including the physical properties, processing characteristics, chemical stability, appearance, and texture of PVC products. Therefore, the purity of calcium powder should be strictly controlled during the production process. So as to ensure the quality and performance of the products.